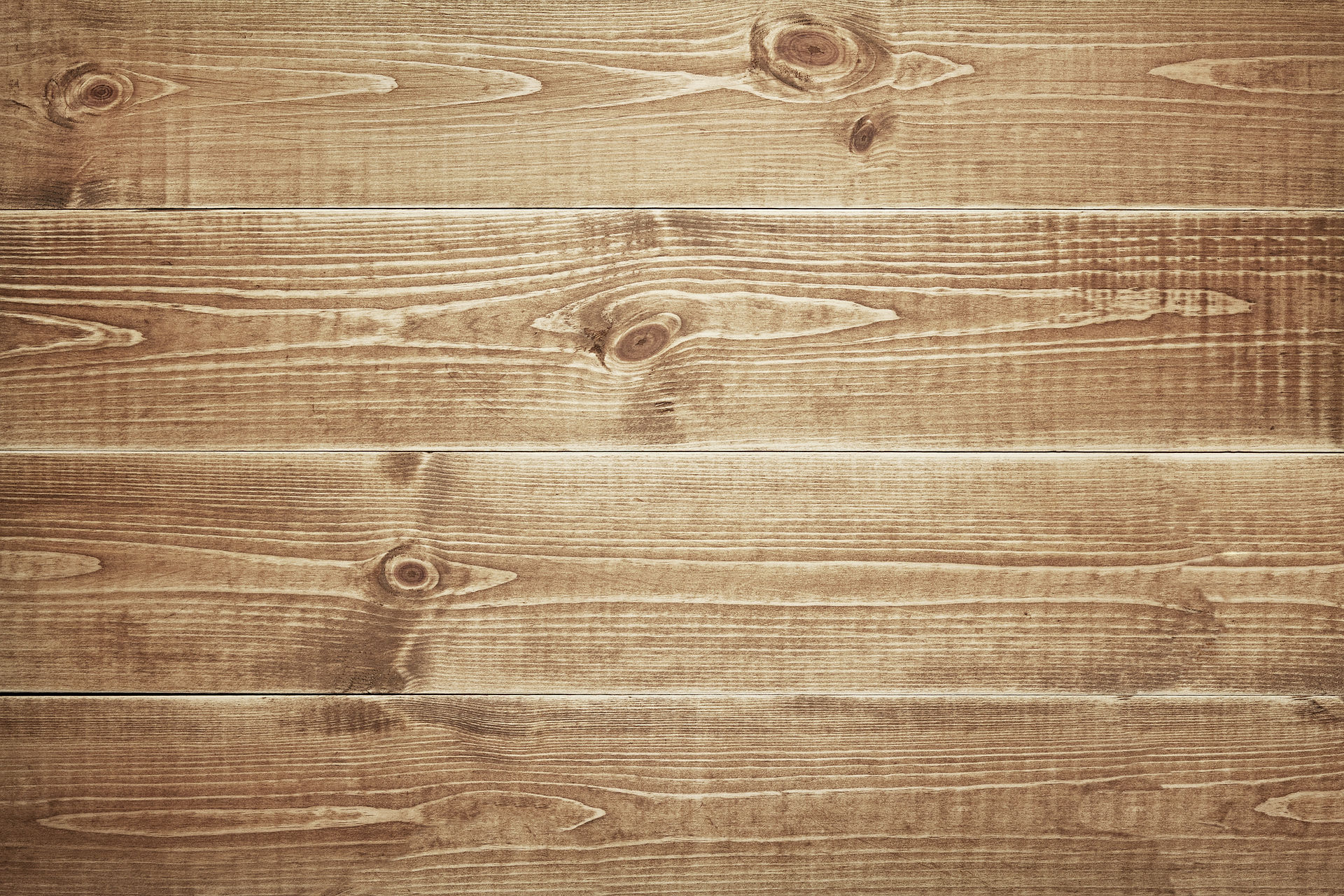
Koptelefoon
Voor dit project mogen we een koptelefoon maken in het blokboek staat dat we uit 4 thema’s moeten kiezen en aan de hand daarvan een ontwerp maken. je kan kiezen uit futuristisch, casual/classic, hipster en uit anime achtig. Ik heb voor de futuristische gekozen omdat me dat een leuke uitdaging lijkt om te ontwerpen en te maken. Na de keuze ben ik begonnen met wat schetsen maken die je ook hieronder kan zien. Wat me opviel op internet als je futuristisch in typt kom je vooral op grote ronde vormen die vloeiend overgaan, maar ook kom je afbeeldingen tegen van dingen die heel recht zijn dus dat is een beetje tegenstrijdig.
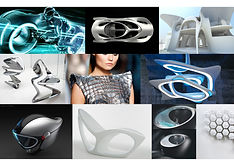
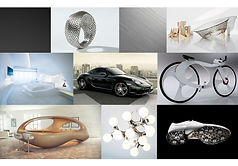
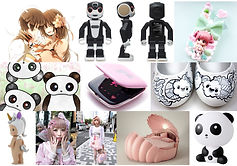



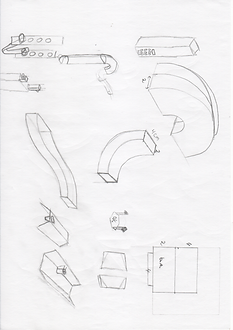
thema's: Tron, Classic, Anime, Vintage
Mijn schetsen voor de koptelefoon
Hieronder zie je mijn concepten die ik gemaakt heb voor het thema futuristisch/tron. Hierbij is bij concept 1 het idee dat je verschillende maten oordelen je erop kan bevestigen. Je hebt namelijk dan on-ear of over-oar. Voor concept 2 is het echt de rechte vormen en dan de krul bovenin van het ronden wat bij dit thema past. Voor concept 3 heb ik meer gedacht aan een meer rechte vormen die meer bij de ruimte past. Hij straalt wat meer stoer uit en robuuster.
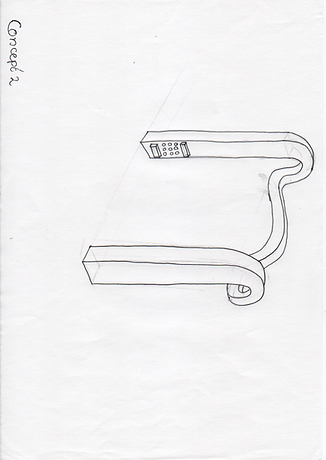



hiernaast kun je het verslagje vinden wat ik met Koen heb besproken over de concepten en welke keuzes er zijn gemaakt.
Conceptkeuze
Voor de definitieve concept keuze ben ik bij Koen geweest. Hij is zeer enthousiast over concept 2 met zijn ronde vormen en is benieuwd hoe ik dit ga produceren. Verder vindt hij het een spannende vorm omdat hem ook doet denken aan de mevrouw van Star-wars door de krul die erin zit verwerkt. Otto zegt dat hij er ook naar uit kijkt hoe dit concept tot zal komen aangezien het niet de normale vormen heeft. Dus van af dit moment ga ik alleen maar werken aan dit concept en ga ik deze verder uitwerken.
Nou is dus het moment van het tekenen in Solid Works van concept 2. Hierbij moet ik gebruik maken van de functie Surfaces. Door deze functie te gebruiken kun je dubbel gekromde vlakken maken die mooi in elkaar overlopen. Dit vond ik best wel lastig aangezien ik het nog nooit gebruikt heb en, omdat Solid Works niet mijn sterkste kant is. Eerst had ik daarom de koptelefoon globaal getekend met boss-extrude en andere functies om zo toch een idee te krijgen van de vormen.
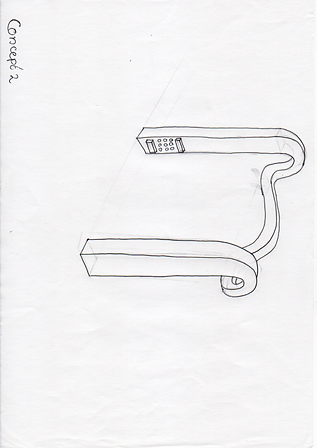


Daarna ben ik begonnen met de functies van Surfaces. Dat lukte mij wel redelijk met ook wat hulp van Joris en Otto. Het probleem wat ik dus nog niet wist is dat je alles in een part moest tekenen en dan vervolgens hoef op te delen in onderdelen. Ik had namelijk alles apart al getekend per onderdeel. Ik wist wel dat ik maar een helft hoefde te tekenen en dan vervolgens de helft kopiëren naar de andere kant.
Uiteindelijk heb ik dus weer een keer opnieuw moeten tekenen en dat resultaat zien je hieronder met de bochten die naar achteren lopen en de opdeling van de onderdelen. Eerst had ik het idee dat de bochten bovenop uit 2 stukken zou moeten gemaakt worden, maar als ik ze rechter zou maken kan ik heel de bovenkant door kunnen laten lopen zodat heel de buitencontour uit 3 onderdelen gemaakt kan worden. Zoals op de foto hieronder kun je de heel de bochten zien en de 2 zijstukken voor op je oren.



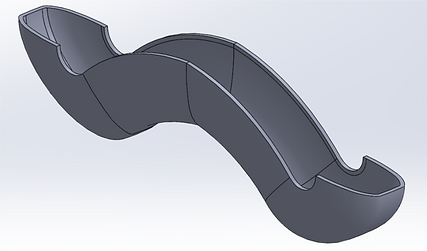
hierboven zie je de rechter en linker kant van de zijkant mijn koptelefoon. verder zie je op de rechter afbeelding de bochten die over je hoofd gaan.
In totaal bestaat de vorm dus uit 6 onderdelen. Hierbij zitten ook de zijplaten en de kromming om de bochten te kunnen afsluiten. Dit heb ik zo gedaan omdat we gebruik moeten maken van de productie techniek vacuum vormen. Daarvoor moeten er schuine randen op zitten en ook afrondingen om hem lossend te hebben. Mijn idee is dus om heel de buitenkant te gaan vacuum vormen. Zowel de 2 zijkanten als de bochten. De platen in de binnenkant wil ik gaan lasersnijden en om de bochten dicht te kunnen maken

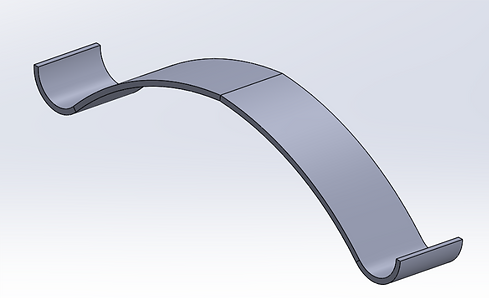
Dit zijn de andere onderdelen die aan de binnenkant van de koptelefoon komen.

Het grootste probleem van het CAD tekenen is eigenlijk om de mal te maken om te kunnen vacuum vormen. Dit lukte me namelijk niet erg goed en hierbij heb ik echt hulp nodig moeten hebben van Otto. Verder heb ik ook aan de zijkanten een randje naar binnen gezet om vervolgens in de ander kant te kunnen schuiven. Het probleem was alleen dat Solid Works daar niet zo goed mee overweg kon. Maar natuurlijk lukt het altijd wel uiteindelijk een keer wat je wilt. zo heb ik dus voor de zijkanten een mal moeten maken, omdat je de bochten moet omdraaien als je hem spiegeld. Verder is ook het grootste onderdeel de bochten die uit een onderdeel gemaakt kan worden.

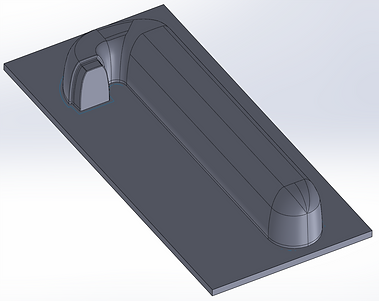
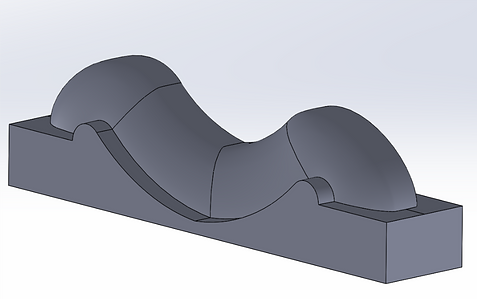
Nu ik de mallen heb gemaakt in Solid Works kan ik ze frezen op de freesmachine. Omdat ik de frees gebruik om daarna te kunnen vacuum vormen hoef ik niet een erg stevig materiaal te gebruiken. Ik kan schuim gebruiken. Dit gaat sneller met frezen en het is goedkoper. Helaas kwam ik erachter dat je ook nog een randje speling nodig hebt aan de bovenkant van de freesmachine. Ook moest ik uitkijken dat de freeskop niet in mijn werk komt als hij ergens onderaan moet frezen. Hierdoor kon ik de file niet in een keer frezen en moest ik hem door de helft doen. Gelukkig is de mal in een keer goed gefreesd.



Zoals je ziet op de afbeeldingen zijn er 2 delen en op een kant heb ik met klei bijgevuld. Dit komt door het blok wat niet recht in de frees lag. Met klei kun je heel mooi weer de afronding afmaken.

Daarna heb ik gelijk de mal gebruikt om de bochten te kunnen maken. Dit heb ik gedaan met de vacuum vormer in de Makerspace. Hiermee verwarm je eerst de kunststof plaat en vervolgens druk je de mal door de plaat omhoog. Vervolgens zuig je de lucht eronder weg en vormt het kunststof om de mal heen. Dit laat je zo 1 minuut aan staan omdat de plaat nog warm is en moet afkoelen. Vervolgens kun je de plaat loshalen en de mal er proberen uit te halen. Eerst heb ik de rand eromheen weggesneden en vervolgens kon ik de mal eruit halen. Hij zat het meest vast tussen de 2 mal delen in. Hij was er namelijk een beetje ingezogen. Dit zie je ook een klein beetje het onderdeel.
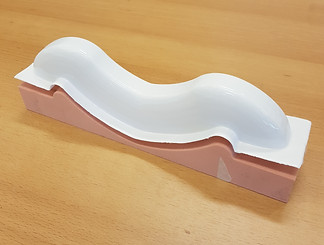
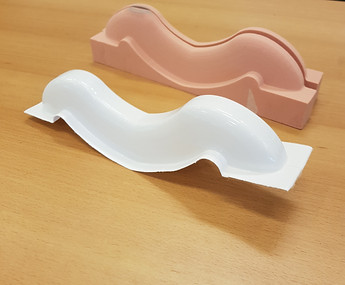

Ook heb ik de zijkanten gefreesd, maar helaas ging dat minder goed dan gedacht. Zoals je hier op de foto’s kunt zien zijn er 3 gemaakt voor de rechterkant. De eerste was het probleem dat de kop van de frees in de mal kwam aan de bovenkant. Hierna heb ik ook de rand aan de bodem dunner gemaakt want daardoor kwam de kop in de mal terecht. Bij de 2e poging ging alles beter maar is de frees in een keer recht naar beneden gegaan zoals je kan zien en is de mal niet meer bruikbaar. De 3e keer is het gelukkig gelukt met de juiste afrondingen. Ook aan de linkerkant is het niet helemaal goed gegaan. Ik wilde namelijk na de eerst grote laag al het afval wegzuigen. Daarvoor moet de frees natuurlijk op pauze staan anders is het levensgevaarlijk. Maar toen ik de frees weer aanzetten ging hij al draaiend naar het begin punt en begon weer opnieuw. Het zal vast wel aan mij gelegen hebben, maar toch heel jammer. Gelukkig kan ik deze mal wel gewoon gebruiken door er ook klei in de gleuf te stoppen.



Hierboven zie je de 2 zijkanten die gefreesd zijn met de linkerkant die opgevuld is met klei.
Hiernaast zie je alle mallen die ik gefreesd heb. zo zie je ook de verloop van goed naar fout bij de 3 rechter mallen.

Speakers
Voor de opdracht van de speakers is dat je ze niet mag vastlijmen/nieten. Daarom heb ik deze houder laten 3D printen waarin hij wordt geklemd. Zoals je op de foto’s ook kunt zien raakt de speaker de tegenhouders niet aan en wordt hij goed geklemd. Ik heb ook nagedacht om klikvingers te gebruiken maar ik wilde eerst deze oplossing gebruiken. Naar mijn mening is dit goed genoeg om de speakers op zijn plek te houden.


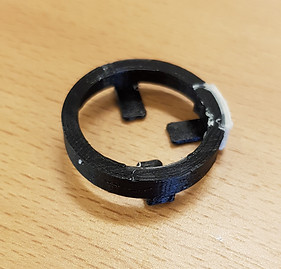
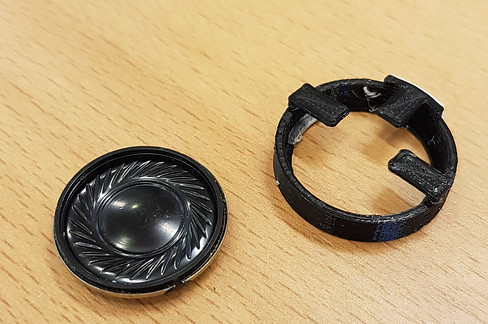
vacuum vormen zijkanten
Ik kon eindelijk mijn zijkanten gaan vacuümvormen na een paar dagen wachten. Voordat je de mal gaat gebruiken moet je ervoor zorgen dat je hem goed hebt ingevet. Dit helpt namelijk om hem later beter los te krijgen. Otto heeft me geholpen bij de machine voor de juiste instellingen. Ik had de machine al eerder aangezet waardoor hij al kon opwarmen. Dus de heaters waren al goed heet toen we de mallen erin deden. Ook kon volgens Otto ook 2 mallen tegelijk uit een plaat gehaald worden. Dat scheelt weer materiaal en tijd. Net als de vorige keer met de boog hadden we de tijd van rond de 110 seconden. Alleen toen stond de heater nog niet zo lang aan. Daar kwamen toen ook achter nadat de plaat al een heel stuk doorgezakt was. Toen hebben we snel de mallen omhoog geduwd en de lucht eronder uit gezogen. Omdat er nu 2 mallen onder 1 plaat lagen is het materiaal ook meer uitgerekt. Dit betekent dat het materiaal dunner is en sneller kapot kan gaan. Toen de plaat was afgekoeld kon ik de mallen eruit halen. Alleen een probleem was dat ze er niet handig uit kwamen of gewoon niet. Zoals op de foto’s hieronder te zien. Eentje heb ik toch nog los gekregen thuis na er enkele keren in geboord te hebben en dergelijk. Jammer genoeg is hij daarbij beschadigd. Het materiaal is ook veel dunner dan dat van het onderdeel van de bochten. Wat aan de bovenzijde van mijn koptelefoon moet komen. Het was dus nog een hele opgave om de mal er weer terug uit te krijgen. Hiervoor moest ik de mal dus wel kapot maken dus die kan ik niet meer gebruiken.
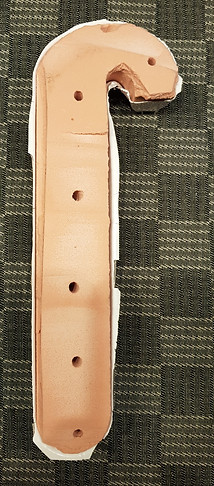
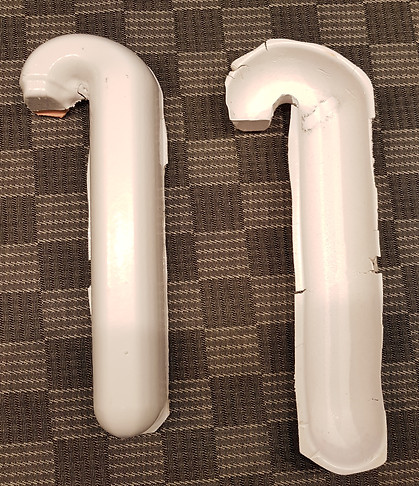

Na deze bevinding moest ik de mallen weer gaan aanpassen in Solid Works. Dat viel dus wel tegen om de files weer aan te passen. Maar het is uiteindelijk toch gelukt. Ik heb ervoor gezorgd dat er aan de bovenzijde een grotere bolling loopt dan de vorige, want dit is waarschijnlijk de reden dat de vorige niet goed lossend waren. Ook heb ik het stukje wat in de bochten moet schuiven aangepast. Deze heb ik namelijk groter gemaakt zodat hij beter aansluit. Helaas heb ik ze nu nog niet opnieuw kunnen frezen.
3D print
Ook heb ik voor op de bovenkant van de bochten een 3D print gebruikt om het aftedichten. Deze kan je zien op de foto’s hieronder. Ik heb de kleur ook in wit gedaan, omdat de koptelefoon zelf ook wit wordt. Alleen moet ik er nog voor zorgen dat hij gelijk komt te liggen aan de rand van de bochten.



Ook heb ik voor de zijkanten van mijn koptelefoon nog dezelfde platen die ik gebruik om te vacuümvormen. Hierbij heb ik flapjes gemaakt die omgevouwen moeten worden waardoor ik ze vast kan maken en gelijk kan leggen met de rand van de zijkanten. Hiervoor moet ik dus wel eerst de onderdelen hebben, maar die moeten dus nog gefreesd worden. Deze wil ik maken door gebruik te maken van de lasersnijder. De voordelen hiervan zijn dat je rechte randen hebt en het naar behoren moet aansluiten van wat je getekend hebt.
Logo en naam
CAD bestand
Voor dit project heb ik ook een naam en logo gemaakt. Hierover kun je meer informatie lezen als je op de knop aan de rechterkant drukt!